
|
 |
 |
Business News | January 2008  
U.S. Auto Crisis Benefits Mexico
Enrique Orellana - InfoAmericas go to original

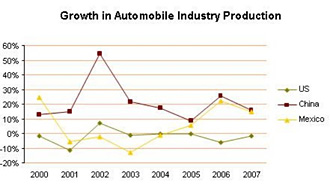
| While auto production in the U.S. and Canada is steadily declining, Mexico’s continues to increase. | | 2007 will be remembered as a historic year for the global automotive industry. For the first time the U.S. was displaced by Japan as the number one vehicle producer in the world, while a Japanese brand, Toyota, overtook GM as the world’s largest carmaker. For the first time in a decade, U.S. car sales will slip below the 16 million mark in 2007, a drop of 1.3 percent over the previous year. The U.S. continues to be the largest market for vehicle sales, but one that is shrinking, and with a recession looming vehicles sales are not expected to recover in the short term.
 RELOCATING TO
 n the face of these trends, U.S. auto industry has embarked on a massive restructuring and downsizing process to reduce costs. Parallel to the downsizing and restructuring, the Big Three are relocating part of their production to lower-cost countries to regain some of their price competitiveness, which is where Mexico comes into the picture.
 While production in the U.S. and Canada is steadily declining, Mexico’s continues to increase. Mexico surpassed the two million unit production mark last year, and is expected to close this year having grown at least 15 percent. This is lower than the 25 percent forecast at the beginning of the year, as Mexico has been negatively affected by the slowdown in U.S. demand, but still a respectable growth rate by global standards. By 2014 Mexico is expected to turnout some 2.7 million units per year (the government projects 4 million units, but these forecast are dismissed by industry experts as unrealistic) and position itself as the world’s fifth largest producer.
 The expansion, fueled by Mexico's largest five automakers–General Motors, Ford, DaimlerChrysler, Nissan and Volkswagen–contrasts with the plans by GM and Ford to cut 60,000 jobs in the United States and close as many as two dozen North American plants by 2012.
 Mexico also leads the pack in new production capacity, with more than $4 billion worth of investments in 2007. Next year will fare even better, with 20 projects announced so far worth together at least $4.4 billion. In comparison, the U.S. has projects for $2.9 billion and Canada for $1.6 billion.
 All major manufacturers in Mexico plan to expand operations, and will together add at least 14 new production lines. Chrysler is leading the investments with a $1.57 billion expansion of its Ramos Arizpe and Toluca plants. General Motors is building a new $650 million plant in San Luis Potosí that will employ 2000 workers by early next year. Ford will begin producing a hybrid model in Hermosillo and will also expand its production plants by an undisclosed amount. Two newcomers are also set to begin production: Toyota will begin assembling its next generation Yaris in a couple years and Hyundai its new Accent model in the state of Veracruz.
 But the most talked about project is the joint venture between Elektra, a Mexican retailer, and China First Automobiles Group, which will begin producing a low-cost vehicle by 2010 in the state of Michoacán. Their plant will initially turn out some 100,000 units targeting the lower segments of the Mexican market, and then turn to also exporting them to Central and South America. With the plant’s presence it is expected that Mexico will attract Chinese auto-parts investments and possibly another manufacturer, India’s Tata Motors.
 MEXICO AS A MAGNET
 In order to grow, U.S. automakers are looking for places to invest where productivity is high and that can generate better returns. Industry analysts believe that Mexico can fit this profile due to its lower production costs and proximity to the U.S., which make the country a natural place for automakers to assemble the next generation of smaller, cheaper cars. Above all, Mexico is attractive because its trained labor is much cheaper. While American assembly workers for Ford and GM in the U.S. make $27 an hour (plus benefits) in Mexico wages in the industry average $3.50 an hour. Although not on the level of American worker, productivity is also rising as a pool of experienced labor and training facilities expand.
 Equally important, the automobile industry in Mexico—now the country’s most important manufacturing sector—has the advantage of possessing a critical mass of auto parts suppliers. Many of these are American brands that have migrated here and now produce $24 billion annually, which creates a well-integrated auto parts supply chain and a just-in-time production capacity, both of which allow costs to be trimmed. This sector has been growing quickly, with 13,500 new positions in last year and a 6 percent growth rate, signaling a bright future.
 Proximity to the U.S. market also means lower transport costs, a key advantage over countries like China. While shipping automobiles from China takes four to six weeks, Mexico can deliver by rail the vehicles in less than one week to anywhere in the U.S.
 Furthermore, under the North American Free Trade Agreement, Mexican-made cars enter the U.S. market without duties, essentially erasing the border for the auto industry. Free trade agreements with other countries, including the European Union, most of Latin America and Japan, mean that a plant in Mexico can ship cars to much of the world with low or nonexistent tariffs, making it an attractive export platform that manufacturers are increasingly exploiting.
 Mexico’s own domestic market is far from negligible in size and scope. Rising income in Mexico and credit expansion bode well for car sales, which will reach 661,000 new passenger vehicles this year. Better still, Mexicans are beginning to trade their subcompacts for higher-value vehicles.
 Mexico is also politically stable, has a comparatively strong intellectual property rights regime and a decent utility infrastructure, all of which contribute to it being a low-risk country to invest in.
 WILL MEXICO LIVE UP TO THE CHALLENGE?
 Despite all of the factors in Mexico’s favor, the country still has some serious issues to deal with that continue to restrain growth. High utility costs, electricity in particular, inflexible labor laws and a fiscal regime that often punishes higher productivity are all negatives. Fiscal, energy and labor reforms are stalled, which has disillusioned many in the industry. The automotive industry in Mexico has also been hit by rising commodity costs such as for steel, aluminum and resin, whose costs are higher in Mexico than elsewhere.
 As well, it is misguided to think that U.S. assembly plants will suddenly and entirely migrate to Mexico or somewhere else. 2008 is an election year and one in which lambasting auto producers for outsourcing to the detriment of American workers will continue to resound. Automakers will try to avoid a political backlash that further relocation plans would cause. In any case, Mexico should not take for granted that Detroit’s carmakers will choose Mexico to cut costs, as they could very well favor countries with large markets where auto sales are booming such as India, Russia and China.
 Even in Mexico the automakers are pressured to cut costs whenever possible. Assembly plants all over the world are trying to cut costs by shifting labor and inventory costs to auto parts suppliers and doing as little as they can themselves. In order to remain competitive, auto parts producers must have cutting edge technology, very efficient logistics and economies of scale to compete with foreigners. In order to meet these conditions, Mexico must have dynamic original equipment manufacturer (OEM) clusters, as logistics and manufacturing efficiencies make all the difference.
 It must also be considered that Mexican production is closely intertwined with the U.S. market and will be negatively affected if the downturn there becomes more severe.
 The Mexican government projects that it can attract as much as an additional $16 billion in the sector over the next five years. Whether this expectation materializes depends on whether Mexico can seize the opportunity and resolve its competitiveness problems. | 
 | |
 |